PHARMACY CLEANROOM SOLUTION — USP 797 & USP 800 Compliant
Ensure full compliance with U.S. regulations for compounding pharmacies with our turnkey cleanroom solutions.
Why U.S. Pharmacies Need USP-Compliant Cleanrooms
Pharmacies in the United States are required to follow USP <797> and USP <800> standards for compounding sterile and hazardous drugs. These regulations aim to ensure the safety of patients and healthcare workers, minimize contamination risks, and control exposure to hazardous substances.
Common pharmacy challenges:
Maintaining ISO-classified environments
Preventing cross-contamination between hazardous and non-hazardous areas
Managing air pressure differentials and airflow
Providing proper gowning and material transfer procedures
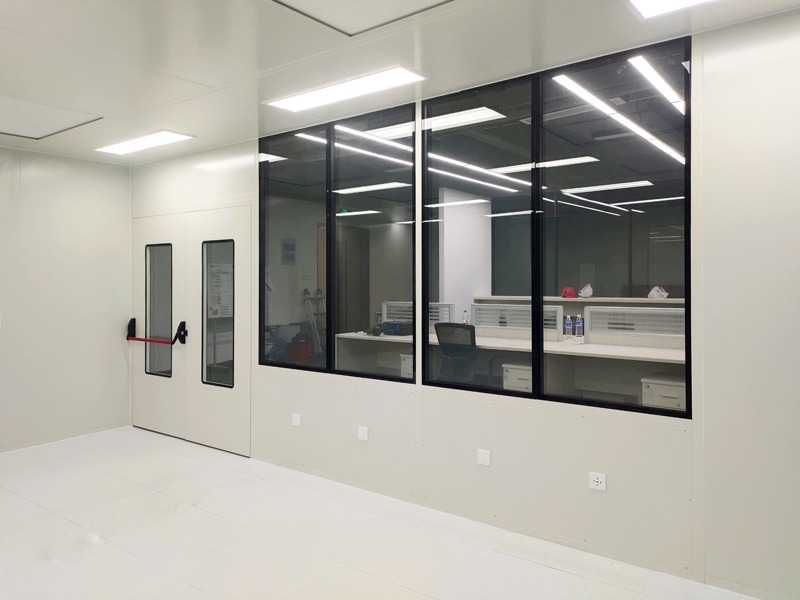


Compliance Design
Follow the standards: Design strictly in accordance with GMP (Good Manufacturing Practice), ISO 14644 (cleanroom standards) and local regulations (such as the Appendix of China’s Good Manufacturing Practice for Pharmaceuticals).
Clean level classification: Determine the clean level (such as A/B/C/D) according to process requirements, for example:
Class A: High-risk operation area (such as aseptic filling).
Class B: Background environment of Class A area.
Class C/D: Non-sterile drug production or auxiliary areas.
Dynamic and static standards: Clarify the particle and microbial limit requirements for production state (dynamic) and empty/static state.
Layout and process optimization
Separation of personnel and logistics: avoid cross contamination, set up independent personnel channels (changing clothes, buffer room) and material channels (transfer window, sterilization facilities).
One-way flow design: use one-way airflow (such as horizontal or vertical laminar flow) in key areas to ensure that pollutants do not flow back.
Functional zoning: clarify the boundaries of clean areas, non-clean areas, and auxiliary areas (such as cleaning rooms and sterilization rooms), and the pressure gradient is reasonable (usually the pressure difference between adjacent areas is ≥10-15Pa).
Air Handling System (HVAC)
High-efficiency filtration: Install HEPA filter (H13-H14 level) at the end, and check for leaks regularly (such as PAO test).
Ventilation frequency: Adjust according to the cleanliness level (such as C level ≥ 25 times/h, D level ≥ 15 times/h).
Temperature and humidity control: Usually the temperature is 18-26℃, and the humidity is 45-65% (special drugs need to be adjusted).
Pressure difference monitoring: Install an online pressure difference sensor and alarm when abnormal.
Materials and surface treatment
Wall/ceiling: Use non-shedding, corrosion-resistant materials (such as color steel plates, stainless steel), and round the corners.
Floor: Epoxy self-leveling floor or PVC seamless floor, anti-static and wear-resistant.
Equipment surface: Smooth, easy to clean, avoid dead corners (such as 304 stainless steel).
Personnel management and training
Changing procedures: strictly regulate the changing procedures (such as changing clothes twice, hand disinfection), and use clean clothes (dust-free materials).
Code of conduct: limit the number of people, avoid violent movements, and prohibit bringing in non-essential items (such as mobile phones).
Training and assessment: conduct GMP and clean room operation training regularly, and take up the post after passing the assessment.

Industry Background & Pain Points
High sterility requirements:
Microbial and particle contamination must be avoided during drug preparation.
High compliance pressure:
Stringent standards such as FDA, EU GMP and USP <797> need to be met.
Difficult expansion:
Existing facilities are difficult to meet the needs of business growth.
Our GMP Pharmacy Cleanroom Solutions
Customized design:
Customize cleanroom layout and functions according to pharmacy needs.
Compliance guarantee:
Cleanrooms comply with FDA, EU GMP and USP <797> standards.
Flexible expansion:
Modular design supports later expansion and upgrade.
