CLEANROOM SOLUTIONS FOR MEDICAL DEVICE MANUFACTURING
Custom-designed clean environments to meet strict industry standards.
Design Considerations for Medical Device Cleanrooms
Creating a cleanroom for medical device manufacturing requires strict adherence to regulatory standards to ensure product sterility, quality, and traceability. Here are the key design considerations and best practices
1. Cleanroom Classification & Compliance
Comply with ISO 14644-1 (typically ISO Class 7–8) or GMP Grade D–C depending on product risk.
Consider process-specific requirements, especially for packaging, assembly, and sterilization steps.
2. Airflow & Filtration System
Use HEPA or ULPA filters to achieve high-efficiency particle removal.
Ensure unidirectional (laminar) airflow in critical areas to prevent cross-contamination.
Design for positive pressure to prevent ingress of contaminants from adjacent spaces.
3. Zoning and Process Flow
Establish clear zoning: clean, semi-clean, and general areas.
Separate personnel flow and material flow to avoid cross-contamination.
Include airlocks, gowning rooms, and pass-through chambers to control transitions between zones.
4. Surface Materials and Construction
Use non-porous, smooth, and chemical-resistant materials such as aluminum panels, HPL, or PVC.
Ensure all surfaces are easy to clean and resistant to microbial growth.
Avoid horizontal ledges or joints where dust and particles could accumulate.
5. Environmental Control & Monitoring
Maintain precise temperature (18–24°C) and humidity (40–60%) control to protect device integrity.
Implement real-time environmental monitoring systems (for particles, temperature, humidity, differential pressure).
Validate and document all environmental conditions for audit readiness.
6. Lighting & Electrical
Use LED lighting with shatterproof covers and anti-flicker functionality.
Ensure flush-mounted fixtures for easier cleaning and minimal turbulence.
Provide anti-static flooring if the product is sensitive to electrostatic discharge (ESD).
7. Compliance & Documentation
Follow FDA 21 CFR Part 820, ISO 13485, and GMP documentation protocols.
Ensure all cleanroom processes are validatable and traceable.
Prepare for regular inspections and certification audits.
8. Personnel Behavior & Hygiene Protocols
Design training spaces and provide standard operating procedures (SOPs) for gowning, cleaning, and entry/exit.
Incorporate hand washing stations, sanitization zones, and visual instructions to maintain hygiene standards.
Why Choose Our Cleanroom?
Building a compliant, high-performance cleanroom for medical device manufacturing requires a partner you can trust.
Here’s why hundreds of clients choose us
1.
Industry Expertise
We have deep experience in delivering ISO/GMP-compliant cleanrooms specifically for Class I–III medical devices.
→ We understand your regulatory challenges, and we build to match them.
2.
Global Project Support
Whether in Asia, North America, or the Middle East, our team provides remote guidance or on-site support for cleanroom installation and training.
→ We’re ready wherever you are.
3.
Turnkey Solutions
We provide end-to-end services: on-site measurement, custom design, engineering, production, trial assembly, shipping, and after-sales support.
→ One-stop service reduces coordination risks and accelerates project timelines.
4.
In-House Manufacturing
Our cleanroom panels, doors, windows, and FFUs are all manufactured in our own ISO-certified facility, ensuring strict quality control, better lead time, and cost-efficiency.
→ You’re dealing directly with the source—no middlemen.
5.
Precision Engineering & Modular Flexibility
Using our proprietary modular system, we deliver flexible and scalable cleanroom spaces that can be expanded, reconfigured, or relocated easily.
→ Future-proof your production environment.
6.
Regulatory Compliance & Validation Support
We ensure compliance with ISO 14644, ISO 13485, FDA CFR 820, and GMP standards, and provide detailed documentation for audits and validation.
→ You get more than a room—you get peace of mind.
Related Cases

Biological Industry Cleanroom——ISO5 70m²
Our biotech cleanroom solutions break through the traditional pharmaceutical cleanliness standards and are designed for cutting-edge fields such as cell and gene therapy, synthetic biology, and microbiome. The use of dynamic pressure gradient control systems and molecular-level air purification technology not only meets the ISO 14644-1 standard, but also achieves precise control of 0.1μm ultrafine particles.Through modular negative pressure isolation units and flexible space layout, we provide biotechnology companies with full-chain environmental protection from GLP laboratories to GMP production.

Pharmaceutical Industry Cleanroom——ISO7 30m²
Cleanroom design includes key control measures such as intelligent personnel/logistics diversion, air lock buffer system, dynamic environmental monitoring, etc., which are suitable for the production and packaging of sterile preparations, biopharmaceuticals, vaccines, injections and highly active drugs. Through full-cycle verification (DQ/IQ/OQ/PQ) and digital environmental monitoring systems, we provide pharmaceutical companies with a safe, reliable and compliant clean production environment, helping to improve drug quality and international market access.

Medical Devices Cleanroom——ISO7 146m²
This project strictly follows ISO 14644 and GMP standards to create a modern clean room that meets the cleanliness level of A/B/C/D. It adopts a high-efficiency HEPA filtration system, precise temperature and humidity control, and laminar airflow organization to ensure that air cleanliness, microbial limits, and environmental parameters continue to meet standards. The clean room design includes key measures such as personnel/logistics separation, strict dressing procedures, and real-time environmental monitoring, and is suitable for the production and packaging of high-demand products such as sterile medical devices, implants, and in vitro diagnostic reagents.
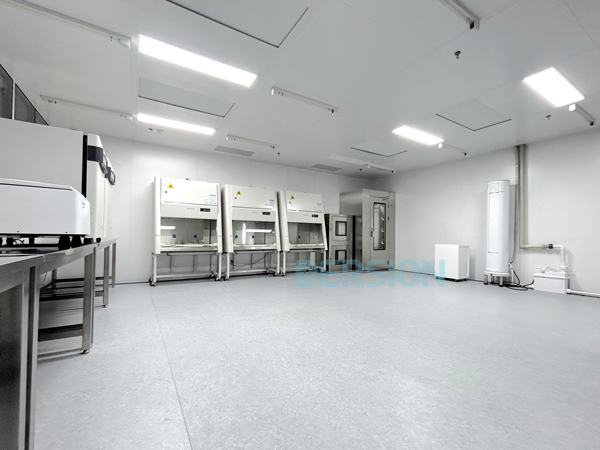
Start Your Cleanroom Project Today
Looking to build or upgrade a [industry] cleanroom?
Contact us for a free consultation.