Clean Room For Biological Industry
The concentration of airborne particles have to be kept as low as possible. The air purity is usually monitored very closely. Here, human beings seem to be the biggest safety hazard for particle contamination. Moreover, machines and assets in a cleanroom are able to completely contaminate optical components, for example,we can use cleanroom in classical optics and micro optics.
APPLICATION
Biological
SIZE
93000.19 sqft
CLEANROOM CLASS
Class100000 / ISO8
Cleanliness Level
The classification of cleanrooms in the biopharmaceutical industry is mainly based on the standards of GMP (Good Manufacturing Practice) and ISO (International Organization for Standardization). The specific levels include:
Grade A: High-risk operation areas, such as filling areas, areas where rubber stopper barrels, open ampoules, open vials, and areas for aseptic assembly or connection operations. A-level cleanrooms must meet the 100-level standard (ISO 5) under both static and dynamic conditions.
Grade B: Background area where high-risk operations such as aseptic preparation and filling are located in the A-level area. B-level cleanrooms must meet the 100-level standard (ISO 5) under static conditions and can meet the 10,000-level standard (ISO 7) under dynamic conditions.
Grade C: Clean operation areas with lower importance in the production of sterile drugs. C-level cleanrooms must meet the 10,000-level standard (ISO 7) under static conditions and can meet the 100,000-level standard (ISO 8) under dynamic conditions.
Grade D: Low-level clean operation areas in the production of sterile drugs. Class D clean rooms only have regulations for static standards, that is, they must meet Class 100,000 standards (ISO Class 8) in a static environment.
Environmental Parameter Requirements
Cleanrooms in the biopharmaceutical industry must also meet the following environmental parameter requirements:
Temperature: Usually between 20°C and 25°C to ensure the stability of chemical reactions and physical processes in the drug production process.
Humidity: Usually between 45% and 65% relative humidity to control microbial growth and prevent drugs from getting damp and deteriorating.
Pressure: Cleanrooms should maintain positive pressure, that is, the air pressure in the cleanroom should be slightly higher than the external environment to reduce the risk of contamination.
Air flow rate: It should meet the requirements of being able to remove particles larger than 0.5 microns to ensure that particles and pollutants are effectively filtered and removed.
Clean Room Design Requirements
The design of a biological clean room needs to fully consider the requirements of microbial control. For example, the layout of a microbiological laboratory should include the P2 main laboratory, the first buffer room, the second buffer room, and the washing and disinfection room to ensure the cleanliness and safety of experimental operators and experimental objects. In addition, the enclosure structure and decoration should also use dust-proof, moisture-proof, and antibacterial materials to ensure the cleanliness and dust-free environment inside the laboratory.
PICTURE SHOW
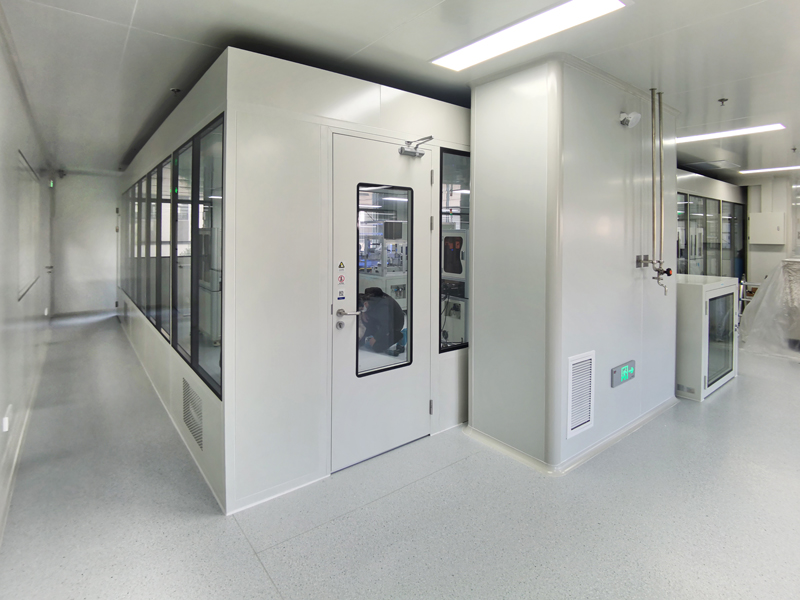
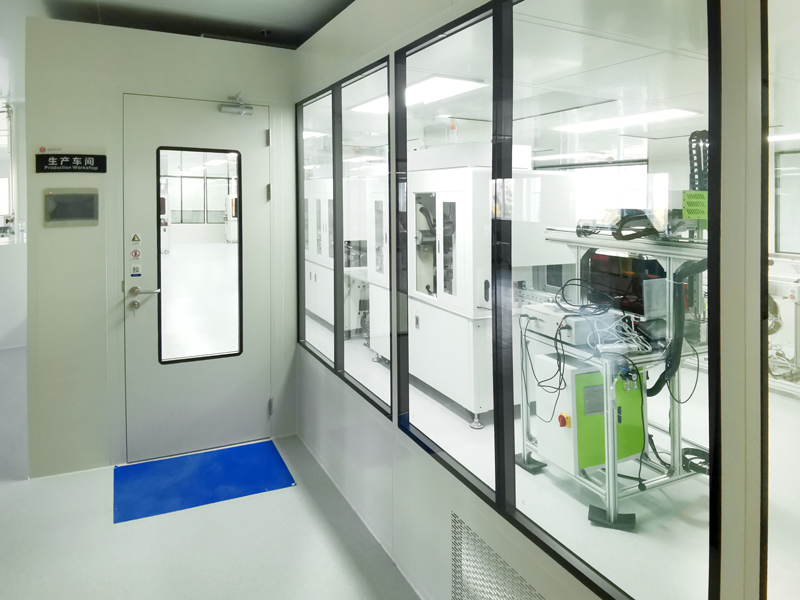
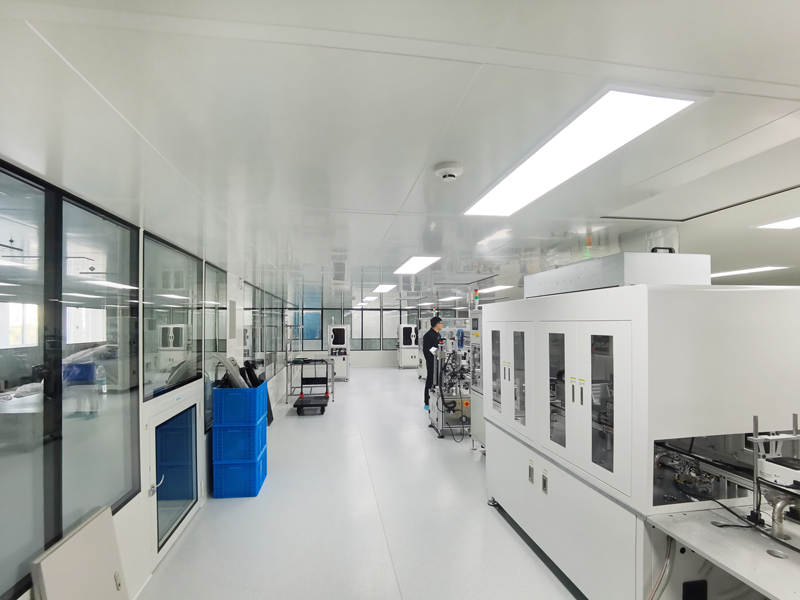
Clean Room Equipment

Clean Room Door
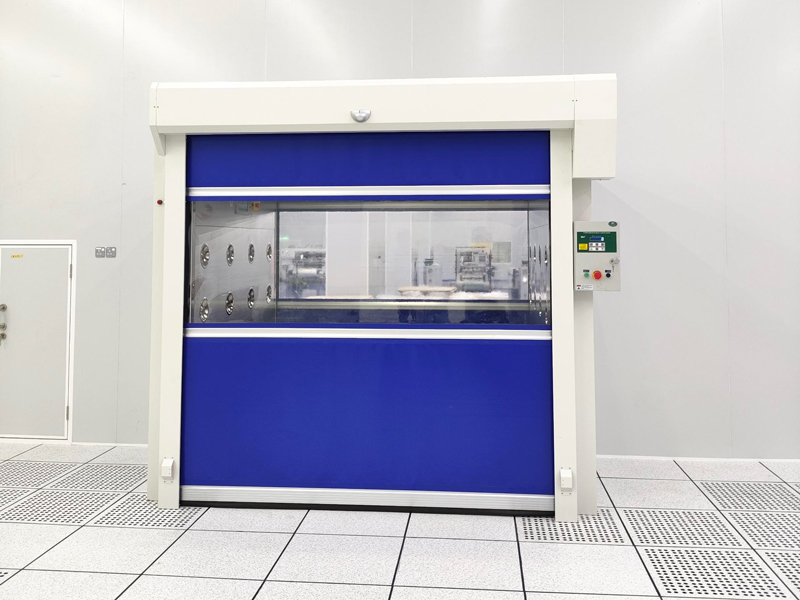
Cargo Shower Room
