As industries across pharmaceuticals, electronics, and medical device manufacturing face growing demands for controlled environments, modular cleanrooms are emerging as a preferred solution. With fast installation, custom design flexibility, and material versatility, modular cleanrooms offer a future-ready alternative to traditional cleanroom construction.
Unlike fixed-build structures, modular cleanrooms are assembled from prefabricated panels and components, enabling rapid deployment and minimal site disruption. “The biggest advantage of modular cleanrooms is the ability to scale and adapt with production needs,” said a spokesperson from DS Cleanroom, a professional manufacturer specializing in cleanroom engineering solutions.
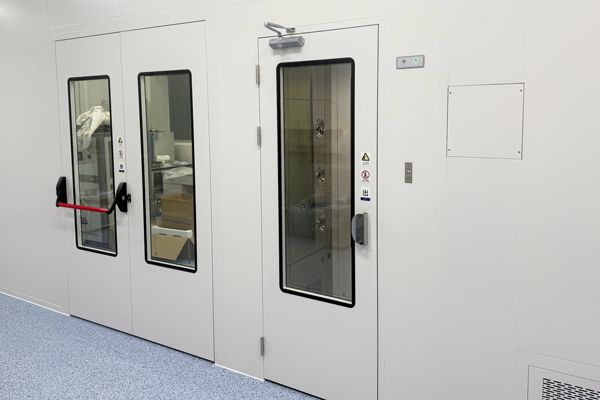
Tailored Cleanroom Configurations
Modular cleanrooms are highly customizable, supporting ISO classifications from Class 5 to Class 8. Customers can specify precise environmental controls, including:
- Temperature range from 15°C to 30°C
- Humidity settings between 30% and 70%
- Positive or negative pressure systems for containment or contamination control
- Custom air changes per hour (ACH) based on the process flow and product type
Layouts can include multiple zones with varying cleanliness levels, such as gowning areas, material pass-throughs, and precision workstations. According to DS Cleanroom, these spaces can be configured in L-shaped, U-shaped, or rectangular formats and even expanded vertically to two stories.
Wide Range of Material and Component Choices
Another key advantage of modular cleanrooms is the wide variety of materials available to meet different regulatory and operational needs. Customers can choose from several wall panel types, including:
- Aluminum honeycomb – Lightweight and fire-resistant
- Rock wool panels – Fire-retardant and thermally insulated
- PU sandwich panels – Economical and easy to assemble
- Stainless steel or color steel – Durable, corrosion-resistant options
- PVC-coated surfaces – Smooth, antibacterial, and easy to clean
Door configurations include hinged, sliding, or automatic types with optional viewing windows and smart access control. Floors can be finished in anti-static PVC, epoxy, or raised structures to support clean air return systems.
Integrated observation windows, interlocking systems, air showers, pass boxes, and HEPA-equipped fan filter units (FFUs) can also be incorporated. Customers may freely select and combine equipment based on room size, layout, and process needs.
Industry Applications and Future Outlook
The flexibility of modular cleanroom systems makes them ideal for a wide range of applications, from pharmaceutical manufacturing and biotechnology to semiconductor assembly and cosmetic production. With increasing emphasis on GMP, FDA, and ISO compliance, manufacturers are seeking faster, more cost-efficient ways to build high-performance clean environments.
“Modular cleanrooms are not just a temporary solution—they’re a scalable, long-term investment,” the DS Cleanroom spokesperson added. “With strong demand for cleanroom solutions globally, we expect modular construction to become the new standard.”
As more companies seek faster setup times, greater flexibility, and lower lifecycle costs, modular cleanrooms are setting a new benchmark in cleanroom engineering.